Key Points Of Dyeing And Finishing Process Of Polyester Stretchable Fabric
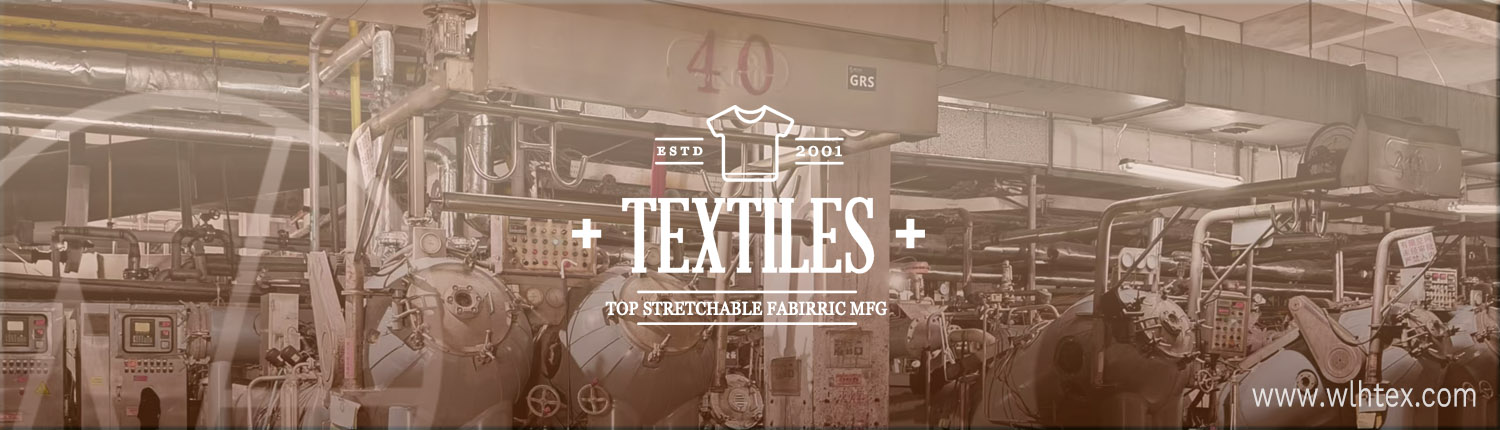
The dyeing and finishing process of polyester spandex warp knitted elastic fabric should mainly focus on the characteristics of spandex yarn and solve the problem of adding more oil agent to spandex yarn in the spinning process. This article takes the example of the polyester spandex warp knitted faabric with 44dtex polyester filament yarn and 44dtex spandex, with the density of 160-220g/m2, and introduces the process and key points of the dyeing and finishing process.
1. Dyeing and finishing process
Unwinding greige fabric – preshrinking (dry cleaning or washing) – preshaping – dyeing – finished product reshaping – inspection – packaging.
2. Pre-treatment
The purpose of pre-treatment is to make the fabric fully relaxed and pre-shrink, eliminate the residual stress inside the fabric, especially the spandex yarn fully retracted, reduce or eliminate the difference of surface density and density inside and outside,on the left, middle and right. At the same time, remove the large amount of fiber oil agent on polyester and spandex yarn, and the oil or other stains on the fabric during the knitting process, in order to facilitate the subsequent work.
Polyester spandex fabric washing process has two kinds of process including laundering and dry cleaning. At present, the mainly adopted process is laundering.Laundry equipment is more cost-effective, with prices about one-third of dry cleaning equipment, and the efficiency of laundering is 15-20% higher than dry cleaning. There are a wider variety of stains that can be washed by washing than by dry cleaning, such as sweat stains when carrying greige fabrics. And dry cleaning is more capable of cleaning oil stains. Water washing uses more water, while dry cleaning is more polluting to the environment. Greige fabrics need to be pre-shaped immediately after washing, otherwise they may create creases in the fabric.
3. Predefinition
In polyester/spandex warp-knitted fabrics, spandex yarns are wrapped inside the fabric by polyester yarns, so they can be thermally shaped like polyester. Generally, it can withstand a relatively quick dry heat treatment of up to 190℃.
The polyester spandex stretch fabric is dipped before preshaping. The purpose is to eliminate the color streaks in the dyeing as much as possible through the antioxidant treatment of the anti-yellowing agent GR.Penetrating agent and defoamer can be added as needed. The pre-shape process condition is generally at 190℃ and the speed is l9-21m/min. The shaping machine employs l0 sections of ovens, with the first 4 sections at low temperature for pre-drying area, which can be set at 160℃, 160℃, 170℃ and 170℃ respectively; the temperature of the last 4 sections of ovens is set at 190℃ and the temperature of the last 2 sections of ovens is set at 180℃. Generally the lower air volume of the shaping machine should be larger than the upper air volume, in order that the fabric surface does not touch either the upper air vent or the lower air vent. The width is generally around 155.2cm; the tension is around 14.7N; the overfeed is around 10%.
The above process parameters should be appropriately adjusted according to the specifications and actual conditions of the greigefabric during production.
4. Dyeing
The polyester spandex stretch warp knitted fabric is generally dyed with disperse dyes in high temperature and high pressure overflow dyeing machine, while the dyeing equipment of nylon spandex stretch plain warp knitted fabric commonly use room temperature rope dyeing machine as well as warp dyeing machine. Considering the influence of temperature on the elasticity, the dyeing temperature is generally set as follows: 120℃ for light color, 125℃ for medium and dark color, 80℃ for reductive cleaning, 40-60min for preservation time, and 1℃/min for lifting temperature rate.
Since the optimal pH value for disperse dyeing is 4.5-5.5, the pH value of the bath is 5.0-6.0 because the disperse dyes are unstable and have poor diffusion performance at pH 7 or higher, and are prone to color blooms and tar spots.
5. Reshaping
When polyester spandex stretch fabric is reshaped, the general temperature used is 180℃, speed at 32-35m/min. The first 4 sections of the oven temperature is low, as a pre-drying area, can be set to 170℃; and the last 4 sections of the oven temperature is set to 180℃. Tension is generally set at 29.4-34.3N. The temperature of nylon spandex fabric is 160℃, and the speed is basically the same as that of polyester spandex fabric.The process parameters should be adjusted according to the fabric specifications and actual conditions.
In addition, compared with nylon, due to less polyester shrinkage than nylon, to get the same finished surface density, such as 200g/m2, polyester stretch fabric generally have to do 195-196g/m2, while the nylon stretch fabric to do 193-194g/m2.