Textile Fabric Shrinkage: Causes and Testing Methods
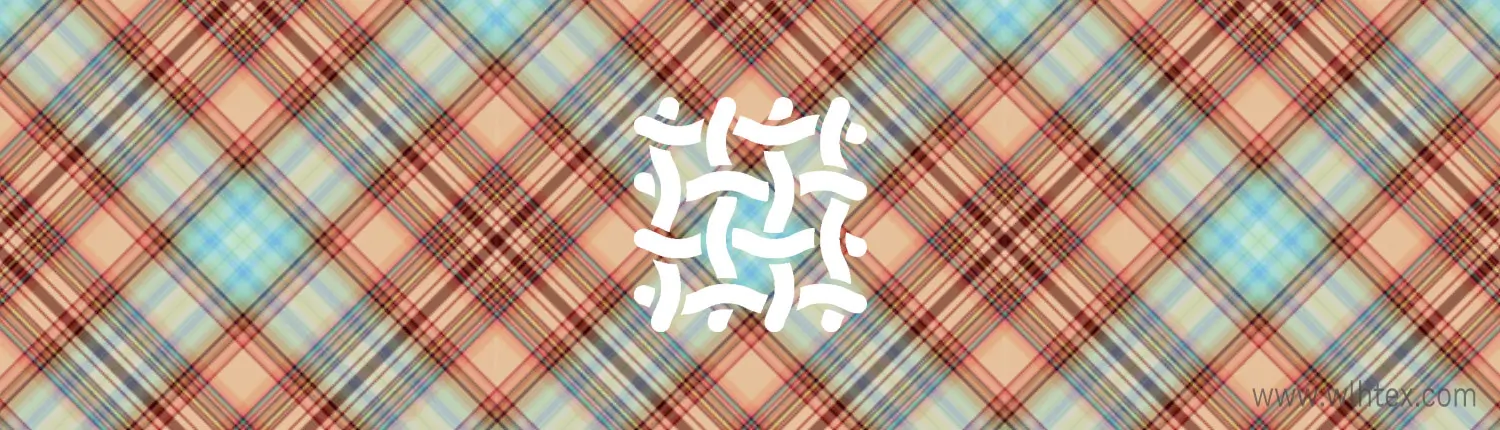
I. Shrinkage Rate: An Overview
Fabrics, composed of textile fibers, undergo a certain degree of swelling when the fibers absorb water, resulting in shrinkage in length and an increase in diameter. Shrinkage rate is typically defined as the percentage of the length difference between a fabric before and after wetting relative to its original length. The stronger the water absorption, the more intense the swelling, leading to higher shrinkage rates and poorer dimensional stability.
The difference between the length of the fabric and the length of the yarn (or thread) used is expressed as the fabric shrinkage ratio (%), calculated as (original yarn length – fabric length) / original yarn length.
Different fabrics exhibit varying shrinkage rates due to differences in their organizational structure and weaving tension. Lower weaving tension results in tighter and thicker fabrics with smaller shrinkage rates, while higher tension produces looser and lighter fabrics with larger shrinkage rates. In dyeing and processing, pre-shrinking techniques are often employed to increase weft density, thus reducing fabric shrinkage rates.
II. Causes of Fabric Shrinkage
① Fibers undergo elongation or deformation during spinning, weaving, and dyeing processes, resulting in internal stress. This stress is released to varying degrees in static dry relaxation, static wet relaxation, dynamic wet relaxation, and full relaxation, allowing fibers and fabrics to return to their initial states.
② Shrinkage degree varies among different fibers and fabrics, primarily depending on fiber characteristics. Hydrophilic fibers, such as cotton, hemp, and viscose, exhibit significant shrinkage, while hydrophobic fibers, like synthetic fibers, show less shrinkage.
③ Fibers swell when wet, increasing their diameter and causing a reduction in fabric length. For example, cotton fibers swell in water, increasing cross-sectional area by 40-50% and length by 1-2%, while synthetic fibers may shrink when exposed to heat, such as boiling water, at approximately 5%.
④ Fibers undergo thermal shrinkage when exposed to heat, and the percentage of length reduction before and after thermal shrinkage is termed thermal shrinkage rate.
III. Shrinkage Rate Testing Methods
Common testing methods for fabric shrinkage include dry steaming and water washing. Using water washing as an example, the testing process is outlined as follows:
① Sampling: Samples are taken from the same batch of fabric, with a distance of at least 5 meters from the fabric edge. The sample should be free of defects that could affect results, and a square of 70-80 cm is cut and left to naturally lay flat for 3 hours. Afterward, a 50 cm * 50 cm sample is placed in the center of the fabric, and lines are drawn around the edges with a marking pen.
② Cutting the Sample: The sample is placed on a flat surface, folds and irregularities are smoothed without stretching, and lines are drawn without applying force to avoid misalignment.
③ Water Washing the Sample: To prevent fading of marked lines after washing, the sample is stitched (for knit fabrics, both sides along the warp, and for woven fabrics, all four sides are stitched). After stitching, the sample is placed in 30-degree warm water, machine washed, dried using a dryer or air-dried, and measured after 30 minutes of full cooling.
④ Calculation: Shrinkage rate is calculated as (dimension before washing – dimension after washing) / dimension before washing * 100%.
Typically, both warp and weft shrinkage rates are measured.
IV. Shrinkage Rates of Different Fabrics
Shrinkage rates vary among different fabrics. Synthetic fibers and blended textiles generally exhibit the smallest shrinkage rates, followed by woolen and linen fabrics, with cotton fabrics falling in the middle. Silk fabrics have larger shrinkage rates, while the maximum shrinkage is observed in viscose fibers, artificial cotton, and artificial wool fabrics.
Shrinkage rates for different fabrics are as follows:
Cotton: 4% – 10%
Synthetic fibers: 4% – 8%
Cotton-polyester blend: 3.5% – 5.5%
Undyed white fabric: 3%
Wool fabric: 3% – 4%
Satin fabric: 3% – 4.5%
Floral fabric: 3% – 3.5%
Twill fabric: 4%
Labor fabric: 10%
Artificial cotton: 10%
V. Factors Influencing Shrinkage Rate
①Raw Materials: Different fabric raw materials result in different shrinkage rates. Fibers with high moisture absorption expand, leading to increased diameter and reduced length, resulting in higher shrinkage rates. For example, viscose fibers can have a water absorption rate as high as 13%, while synthetic fibers exhibit lower moisture absorption and, consequently, lower shrinkage rates.
② Density: Fabric density influences shrinkage rates. Fabrics with similar warp and weft densities exhibit similar shrinkage rates. Higher warp density results in higher warp shrinkage, and conversely, fabrics with higher weft density than warp density show higher weft shrinkage.
③ Yarn Thickness: Yarn thickness affects shrinkage rates. Fabrics with thicker yarns have higher shrinkage rates, while fabrics with finer yarns have lower shrinkage rates.
④ Production Process: The production process of the fabric influences shrinkage rates. Fabrics that undergo multiple stretches, have a longer processing time, and experience higher tension during weaving and dyeing processes exhibit higher shrinkage rates.
⑤Fiber Composition: Natural fibers (e.g., cotton, linen) and regenerated plant fibers (e.g., viscose) exhibit higher moisture absorption and swelling, leading to larger shrinkage rates. Wool, with its scale-like surface structure, is prone to felting, affecting dimensional stability.
⑥ Fabric Structure: Generally, woven fabrics exhibit better dimensional stability than knit fabrics, and high-density fabrics have better stability than low-density ones. In woven fabrics, plain weaves typically have smaller shrinkage rates than flannel weaves, while in knit fabrics, plain knits have smaller shrinkage rates than ribbed knits.
Production and Processing: During dyeing, printing, and finishing processes, fabrics are inevitably subjected to machine stretching, creating tension in the fabric. Upon contact with water, fabrics easily release this tension, leading to shrinkage. Pre-shrinkage is commonly used in the manufacturing process to address this issue.
⑦ Washing and Care Processes: Washing and care processes, including washing, drying, and ironing, impact fabric shrinkage. For example, hand-washed samples generally exhibit better dimensional stability than machine-washed samples, and washing temperature also affects shrinkage rates. In general, higher temperatures result in poorer stability.
Drying Method: The drying method significantly affects fabric shrinkage. Common drying methods include drip drying, metal mesh flat drying, hanging drying, and drum drying. Among these, drip drying has the least impact on fabric dimensions, while drum drying has the greatest impact, with the other two methods falling in between.
Ironing Temperature: Choosing an appropriate ironing temperature based on the fabric composition can improve shrinkage. For example, cotton-linen fabrics can benefit from high-temperature ironing to reduce shrinkage. However, higher temperatures may not be suitable for synthetic fibers, as they can damage the fabric’s properties, leading to stiffness and brittleness.
Understanding these factors and conducting thorough testing can help manufacturers and consumers better manage and predict fabric shrinkage, ensuring the longevity and performance of textiles.